Advances in Asphalt Shingle Technology
Submitted by: Eileen Dutton, chair of the Steep Slope Committee for ARMA
This year marks an important point in asphalt roofing history. The Asphalt Roofing Manufacturers Association (ARMA) is celebrating its 100th anniversary throughout 2015. Since its inception, the trade association has brought together the majority of North American manufacturers and their raw material suppliers to promote asphalt roofing. The industry has also come together to continuously improve asphalt products through technological advances and scientific research. ARMA’s centennial presents a unique opportunity to look back on more than 100 years of industry advancement, and look ahead to what exciting technologies asphalt roofing will utilize in the future. This article will focus on asphalt shingle advancements over the past 125 years.
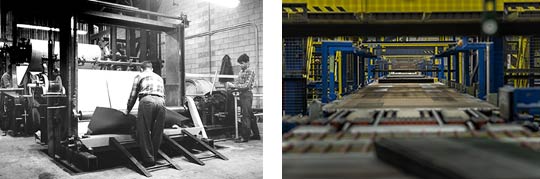 |
Asphalt shingle manufacturing processes have changed dramatically over the past 125 years. |
Asphalt has been used as a roofing material since roll roofing hit the market in 1893. The 19th century product would be virtually unrecognizable to modern asphalt shingle manufacturers, whose companies continue to improve upon shingles and develop today’s high-value, high quality products. When asphalt shingles were first introduced, cotton rag was used as the reinforcement material. When cotton rag was in short supply, other organic materials, such as wood pulp or paper, were used to reinforce asphalt shingle products. This created what became known as organic reinforcement, or felt, which was saturated and coated with asphalt. These early shingles were coated with various materials, including crushed slate or oyster shells, and have progressed over time to the brightly colored ceramic-coated granules that we see today.
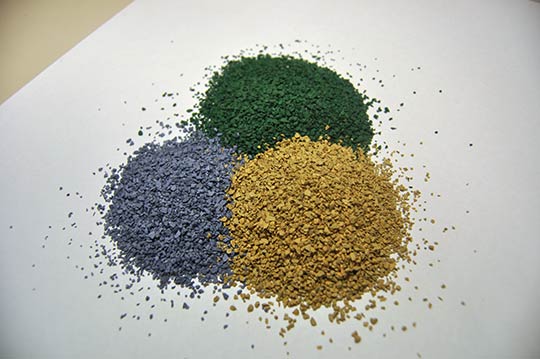 |
Today, shingles are coated with granules that come in a variety of colors. |
In the 1970’s, fiberglass began to be used as the reinforcement for both built up roofing (BUR) and shingles, yielding a stable reinforcement that was stronger and would not shrink or tear as some of the organic felt products did. Fire resistance was also improved because of the use of fiberglass reinforcement— fire-resistance ratings improved from a typical Class “C” to Class “A” for shingles, the highest rating available. The fiberglass mat also helped curb the curling and decay issues associated with cotton and organic shingles.
The first asphalt shingles were pre-fabricated, single-cut pieces of material that could be field installed faster than building a roof in place. Over time they advanced to single layer materials cut into two or more tabs, some with large exposures and typically with very few colors. Today’s shingles come in many formats, from single-layer shingles with no cutouts to those with multiple cutouts, and from standard laminated shingles of multiple thicknesses to the newer, open tab designer shingles. Slate or shells were first added to protect the asphalt from UV aging, but still resulted in fairly monotonous colors. Today, color experts help to design shingles, taking them from the dull colors of the 1970’s to the numerous vivid colors now available. Modern asphalt shingles come in enough colors and styles to match the unique design of any home. Whether a homeowner wants brown, black, blue or anything in between, there is an asphalt shingle to fit their needs. The use of color and design in asphalt shingle technology is also being used to mimic more costly materials such as slate, wood and tile.
Advances in granule technology have also helped to mitigate the issues of algae discoloration and heat build-up in attic spaces. Asphalt roofing manufacturers have developed special granules that can help keep a roof free from algae for many yearsi. Special pigments, originally developed to lower the heat signature of military planes and tanks, have been added to the ceramic coated granules. The special pigments increase the overall reflectivity of the shingles, which may help lower the building’s air conditioning requirements, especially on buildings where there is minimal insulation.
Developments in sealant technology have also been used to address various roofing issues. Sealing strips were added to shingles in the 1950’s to improve wind resistance and reduce installation time by eliminating the need to hand tab shingles. Testing procedures have also advanced. Standard wind-resistance testing has advanced from using a high speed fan running at 60-mph up to one going 110-mph (UL997 / ASTM D3161).
In 1997, the Asphalt Roofing Manufacturer’s Association (ARMA) wanted to see if there was a better predictor for wind uplift than the standard fan test, and worked with Colorado State University’s Dr. Jon Peterka to study the wind uplift pressures on shingles.ii This resulted in two new test methods, ASTM 6381,iii “Standard Test Method for Measurement of Asphalt Shingle Mechanical Uplift Resistance” and the D7158, “Standard Test Method for Wind Resistant Asphalt Shingles with Sealed Tabs.” These are the test methods cited in the International Residential Code and International Building Code.
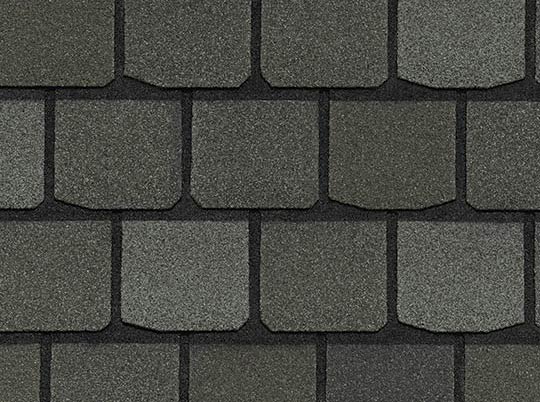 |
Advances in asphalt shingles have made them not only affordable, but able to protect your home from the elements. |
Changes have also been made to shingles to improve wind uplift resistance. The sealant strip was moved closer to the edge of the shingle, and the sealants themselves were improved. The traditional wind sealant formulation was a specialty oxidized asphalt sealant. In the 1990’s to mid-2000’s, the use of modified asphalt sealants started with the intent to improve the overall temperature properties of the wind sealant strip. It was found that polymer modified asphalt adhesives improved the holding performance of the shingle and lengthened the time the sealant stays flexible and active on the roof.
Laminating adhesives improved from a standard oxidized adhesive to a polymer modified version around the mid-2000 time period. Improperly nailed laminate shingles with an oxidized sealant would tend to slide on the roof if they were not fastened exactly in the correct location. The use of polymer modified laminate adhesive improved the high temperature slide characteristics of the laminate shingle. Even though the laminate adhesive has been improved, it is still important and required by manufacturers to fasten shingles in the nail zone. Wind resistance has always been a consideration with shingles, but hail has come to the forefront of shingle design in recent years.
According to a 2003 articleiv in Insurance Journal South Central Magazine, certain roofing materials were known to function better in hail events than others. Armed with that knowledge, the Institute for Business and Home Safety (IBHS) worked with Underwriters Laboratories (UL) to create a test standard, UL 2218, “Impact Resistance of Prepared Roof Covering Materials,” to test the impact resistance performance of roofing materials. The test classifies materials as Class 1 through 4, with Class 4 materials being the most impact resistant. Class 4 materials are resistant to a 2” steel ball dropped from a height of 20 feet. While these more advanced tests were being developed, the asphalt roofing industry began to approach the problem of hail damage in different ways.
One improvement to impact resistance was to modify the asphalt with SBS polymers, creating a polymer modified shingle. According to the Insurance Journal South Central Magazine article, polymer modified shingles are stronger and more flexible than standard shingles. Standard oxidized shingle manufacturers began to look for ways to improve resistance to hail as well, which included reinforcement improvements, and typically adding a scrim or polyester backer to reduce the impact. IBHS post-storm investigations show that Class 4 impact shingles perform better than non-impact resistant shingles.
Over the past century, asphalt shingle manufacturers have used research and technology to specifically address roofing issues and create an even better product. Improvements in aesthetics, wind and hail resistance, and solar reflectivity have kept asphalt shingles the most popular choice in America, with four out of five homeowners choosing asphalt shingles.
.jpg) |
Asphalt roofing remains a top choice for homeowners in the United States. |
As ARMA celebrates its 100th anniversary this year, the organization urges consumers and the industry to remember that asphalt shingles aren’t what they were a century ago. Deliberate advances through research and development have made asphalt shingles an ever-changing, technologically innovative product. This high level of innovation ensures that there are many more exciting changes to come throughout the next 100 years.
For more information on asphalt roofing, please visit www.asphaltroofing.org.
i J.L. Jacobs and R. Thakur, “How Advances in Algae-resistant Roofing Address the Growing Roof Algae Problem,” 4th International Symposium on Roofing Technology, National Roofing Contractors Association, September 1997, p. 99.
ii Peterka, J., Cermak, J., Cochran, L., Cochran, B., Hosoya, N., Derickson, R., Harper, C., Jones, J., and Metz, B. (1997). “Wind Uplift Model for Asphalt Shingles.” J. Archit. Eng., 3(4), 147–155.
iii asphaltshingles.windengineer.org/?page_id=854
www.astm.org/Standard/standards-and-publications.html
iv Binion, T., “Let It Hail, Let It Hail, Let It Hail!”, April 2003, Insurance Journal South Central Magazine www.insurancejournal.com/magazines/features/2003/04/07/28144.htm
|